Dr. Klaus Seppeler Stiftungspreis
für Robert Muggleton
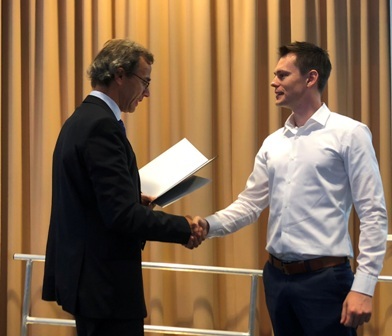
Hr. Prof. Feser mit Hrn. Robert Muggleton bei der Preisverleihung
Zum vierzehnten Mal wurde auf der Mitgliederversammlung am 06. November 2018 der Stiftungspreis verliehen an Robert Muggleton für seine Arbeit zum Thema: CO2 Preferential Weld Corrosion of Longitudinally Welded Linepipe: Effect of Microstructure, Corrosion Product Layers, and the Environment
The doctoral thesis of Robert Muggleton focused on the preferential weld corrosion of ERW longitudinally welded linepipes in CO2 containing production environments. Preferential weld corrosion has plagued the oil and gas industry for decades, with the literature consensus focusing on chemical composition differences between the weld metal and base metal as the primary cause. The argument is that if the weld filler metal is less noble than the base metal, a galvanic couple will establish where the weld metal becomes the anode and preferentially corrodes. Unfortunately this reasoning is not able to explain all cases of preferential weld corrosion. Longitudinally welded ERW linepipe is a popular material choice for its lower costs and shorter lead times over seamless linepipe. As with all welding processes the high heat input causes several microstructural zones to be present around the ERW weld region. However, the ERW weld is autogenous (does not use a welding consumable), therefore the weld metal, the heat affected zone (HAZ), and the base metal have identical chemical compositions. From the literature consensus, one would expect these linepipes to be resistant to preferential weld corrosion as there are no galvanic driving forces, however industry experience shows otherwise. The industry observation is complicated as often flowlines are made from the same material grade (e.g. X42), however sourced from several manufacturers. After a few years of operation, some manufacturers appear to be immune to preferential weld corrosion while others appear highly susceptible, despite both operating in identical conditions. Rob’s thesis was the first investigation that looked the pure ability of microstructure to form strong galvanic coupling currents that lead to preferential weld corrosion.
The developed technology allowed the investigated ERW linepipes to corrode in a natural and unforced way in various production environments inside a stirring autoclave, however, the galvanic coupling currents flowing between the different microstructural zones present in the ERW linepipes could be monitored in real time. This allowed direct identification of microstructural zones present in each ERW linepipe (i.e. manufacture) that were susceptible to localized attack. Scanning electron microscopy revealed that susceptibility to localized attack was directly linked to the local corrosion product morphology that formed on each microstructural zone present in the ERW weld. The results showed that during the initial stages of corrosion the galvanic coupling currents between the different microstructural zones were negligible; this was expected as the chemical compositions were identical. However, after several days different microstructural zones started to form morphologically different corrosion product layers, and this then formed strong galvanic coupling currents (in the mm/y range) for certain manufacturers. The formation of morphologically different corrosion product layers was heavily dependent on local grain size and cementite morphology.
Rob’s dissertation clearly showed that even if the chemical composition of the weld metal, HAZ, and base metal were identical, localized differences in microstructure were capable of forming strong galvanic coupling currents that led to preferential weld corrosion. As a result, clear guidelines were developed for avoiding preferential weld corrosion in longitudinally welded linepipes, and the developed technology was proven to be a powerful tool for material selection and manufacturer qualification.